Polymer Nanocomposite Materials
(i) Designing Superior Polymer-Grafted Nanoparticle Thin Films for Ballistic Applications: The goal of this sub-project is to develop a computational framework to understand molecular processes in polymer-grafted nanoparticle (PGN) thin films under ballistic loadings and obtain optimized design parameters for their superior ballistic performance.
PGNs have shown a paradigm shift in material design because of their enhanced thermal, mechanical, or electrical properties compared to neat polymers. Due to its large design space, including nanoparticle (NP) core radius (, polymer graft density (), polymer chain length () and polymer chemistry, PGNs can be tailored for high strength or high toughness. A PGN system with high and low shows a very ordered structure and high strength but it is brittle in nature. On the other hand, low and high lead to an increase in toughness as the polymer chains from NPs intermingle with each other whereas the modulus approaches the value of its neat polymer. Therefore, with a careful selection of design parameters, it is possible to obtain higher strength and toughness simultaneously, which makes PGN thin films a suitable candidate for shock absorption and ballistic impact applications as both of these properties are required for superior ballistic performance. However, to do that, we need a better understanding of how different parameters affect thin film’s mechanical properties as well as a parametric sweep of the design space to attain optimized values.
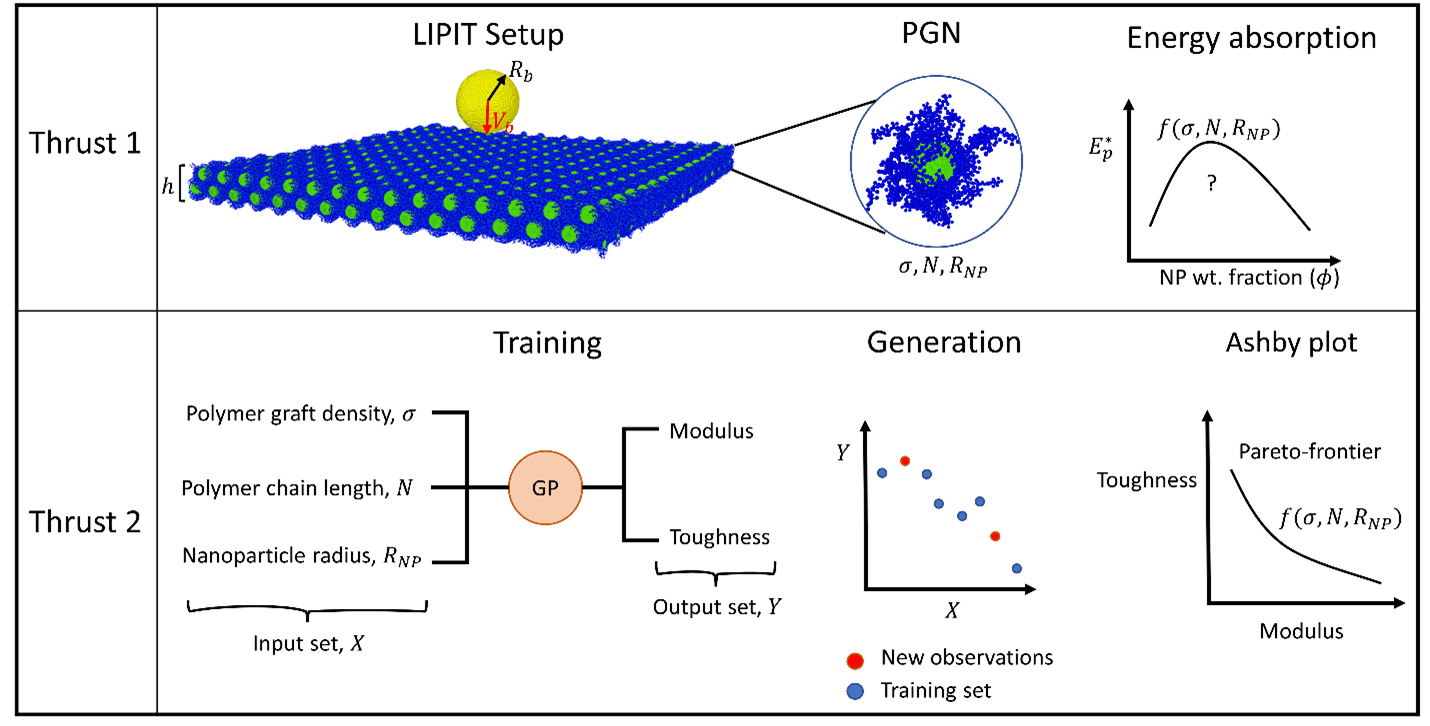
(ii) Developing interaction potential for polymer-grafted nanoparticles:
Matrix-free nanocomposites made from polymer-grafted nanoparticles (PGN) represent a paradigm shift in materials science because they greatly improve nanoparticle dispersion and offer greater tunability over rheological and mechanical properties in comparison to neat polymers. Utilizing the full potential of PGNs requires a deeper understanding of how polymer graft length, density, and chemistry influence interfacial interactions between particles.
There has been great progress in describing these effects with molecular dynamics (MD). However, the limitations of the length and time scales of MD make it prohibitively costly to study systems involving more than a small number of PGNs, even with bead–spring coarse-grained models. Moreover, it remains unclear how to properly address the shortcomings of these models in describing the rate-dependent constitutive response of polymers in a chemistry-specific fashion. Here, we address some of these challenges by proposing a new modeling paradigm for PGNs using a strain-energy mapping framework involving the potential of mean force (PMF) calculations.
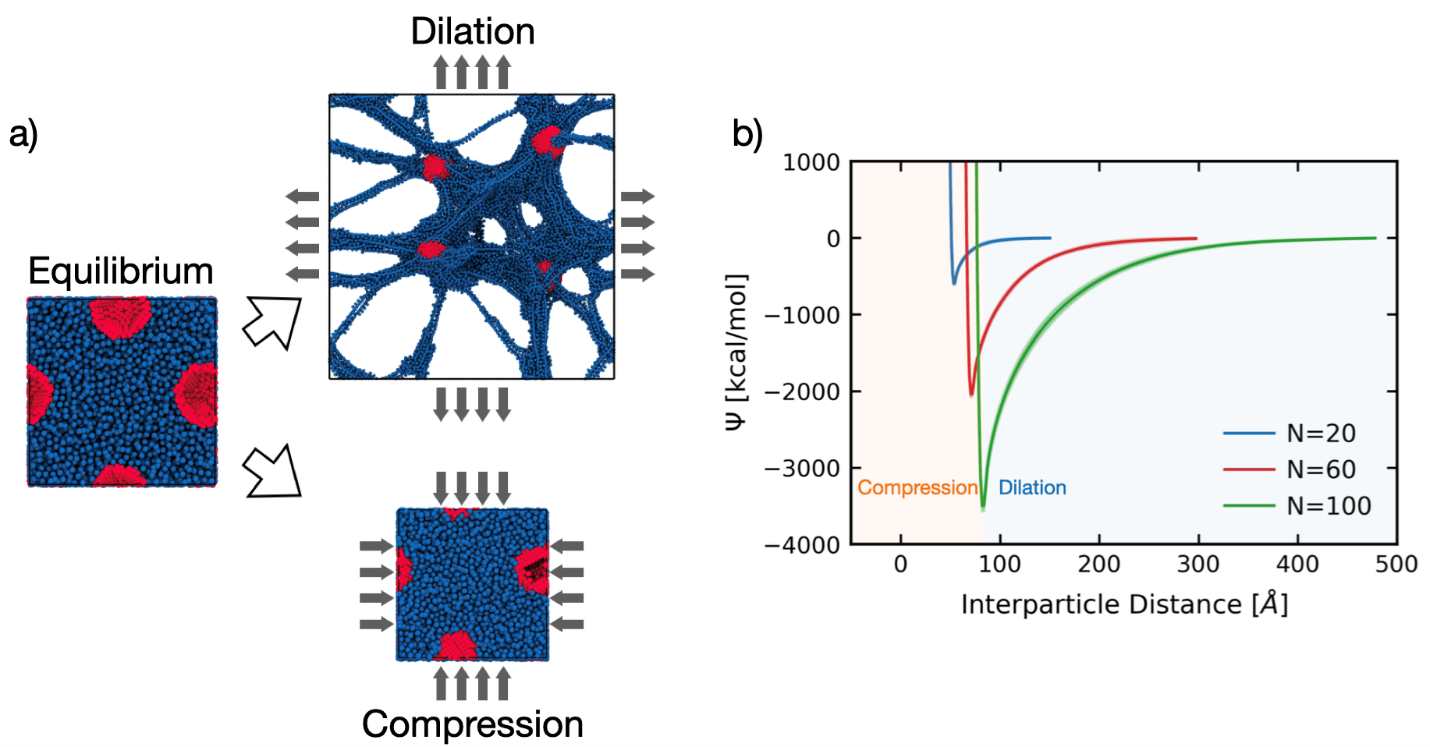
Fig. (a) Schematic of dilation/compression deformations from PMMA PGN melts at equilibrium in the CG-MD representation. (b) Examples of the potential of mean force (PMF) as a function of interparticle distances derived from CG-MD models of PGN melts with graft chain length N = 20 monomers (blue), N = 60 monomers (red), and N = 100 monomers (green). The repulsive and attractive potentials from the compression and dilation deformations are separated by light orange and blue backgrounds, respectively, for PGN melts with N = 100 monomer.
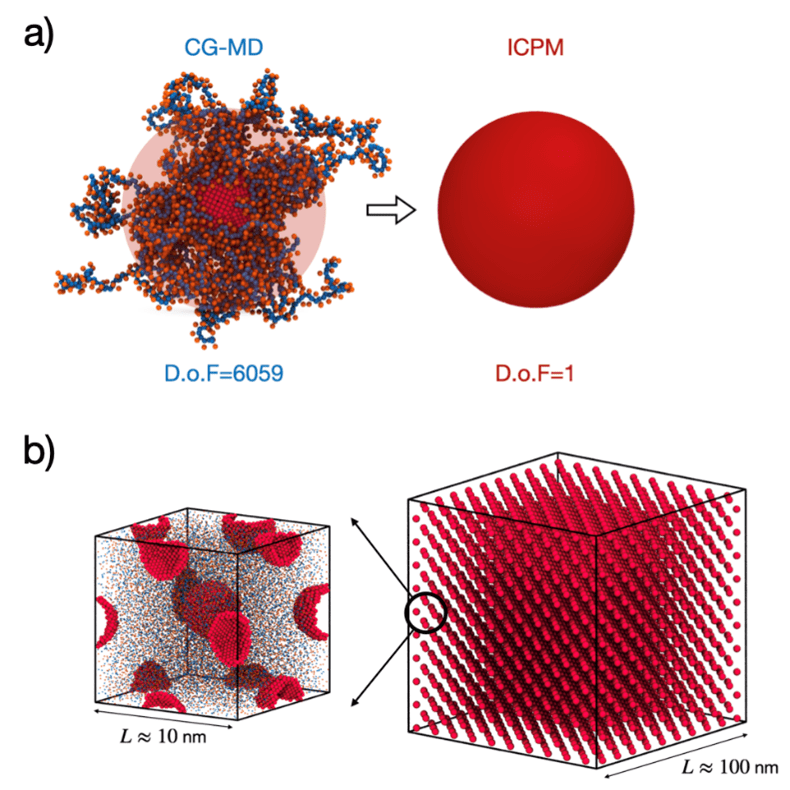
Fig. (a) Coarse-grained mapping scheme from a CG-MD model to an ICPM of a single PMMA–PGN with graft length N = 100 monomers. Blue, orange, and red beads represent the polymer backbone, side groups, and nanoparticle surface beads, respectively. Accordingly, the number of simulated particles decreases from 6059 (beads) in CG-MD to 1 (bead) in the ICPM. (b) A unit cell of matrix-free PGNs with graft length N = 100 monomers in the CG-MD representation, and a simulation box comprises multiple unit cells in the ICPM representation.
Achievements:
- Each nanoparticle is coarse-grained into a representative particle with chains treated implicitly, namely, the implicit chain particle model (ICPM).
- A chemistry-specific coarse-grained molecular dynamics (CG-MD) model of poly(methyl methacrylate) is used as the reference system.
- The effective interaction between particles is derived by matching bulk dilation and compression strain-energy densities up to failure.
- The model can accurately quantify the effect of strain-rate dependence with the simple power-law Cowper–Symonds strain hardening model.
- Due to the aggressive degree of coarse-graining (∼1:10 000), the overall, increase in the computational speed by approximately 5–6 orders of magnitude compared to the CG-MD models.
- This novel framework is foundational for particle-based simulations of PGNs and their blends and accelerates the understanding and predictions of emergent properties of PGN materials.
Relevant papers:
- Wu, Zhenghao, Subhadeep Pal, and Sinan Keten. “Implicit Chain Particle Model for Polymer-Grafted Nanoparticles.” Macromolecules9 (2023): 3259-3271.
(iii) Investigating the mechanical properties of polymer-grafted nanoparticles: Polymer-grafted nanoparticle (PGN) materials hold the potential to show greatly enhanced mechanical properties over neat polymer melts. PGNs offer an extremely large parameter space through nanoparticle size and shape, grafted chain lengths, grafting density, and polymer chemistry. We have worked to investigate how the effects of these factors play into the mechanical enhancement of PGNs. We have contributed to developing accurate coarse-grained molecular dynamics simulations to characterize bulk PGN material response to mechanical loadings including tensile and shear forces. For example, such characterization has shown correlations such as an increased nanoparticle volume fraction directly contributing to the enhanced complex shear modulus response of PGN systems. Additionally, using particle-based simulation methods has allowed us to develop theory in grafted polymer chain dynamics, fatigue response, and nanoparticle dispersion to help understand and explain mechanical phenomena of interest. In addition to this work, our group has collaborative efforts in the mechanics of PGN membrane systems designed for gas transport challenges.
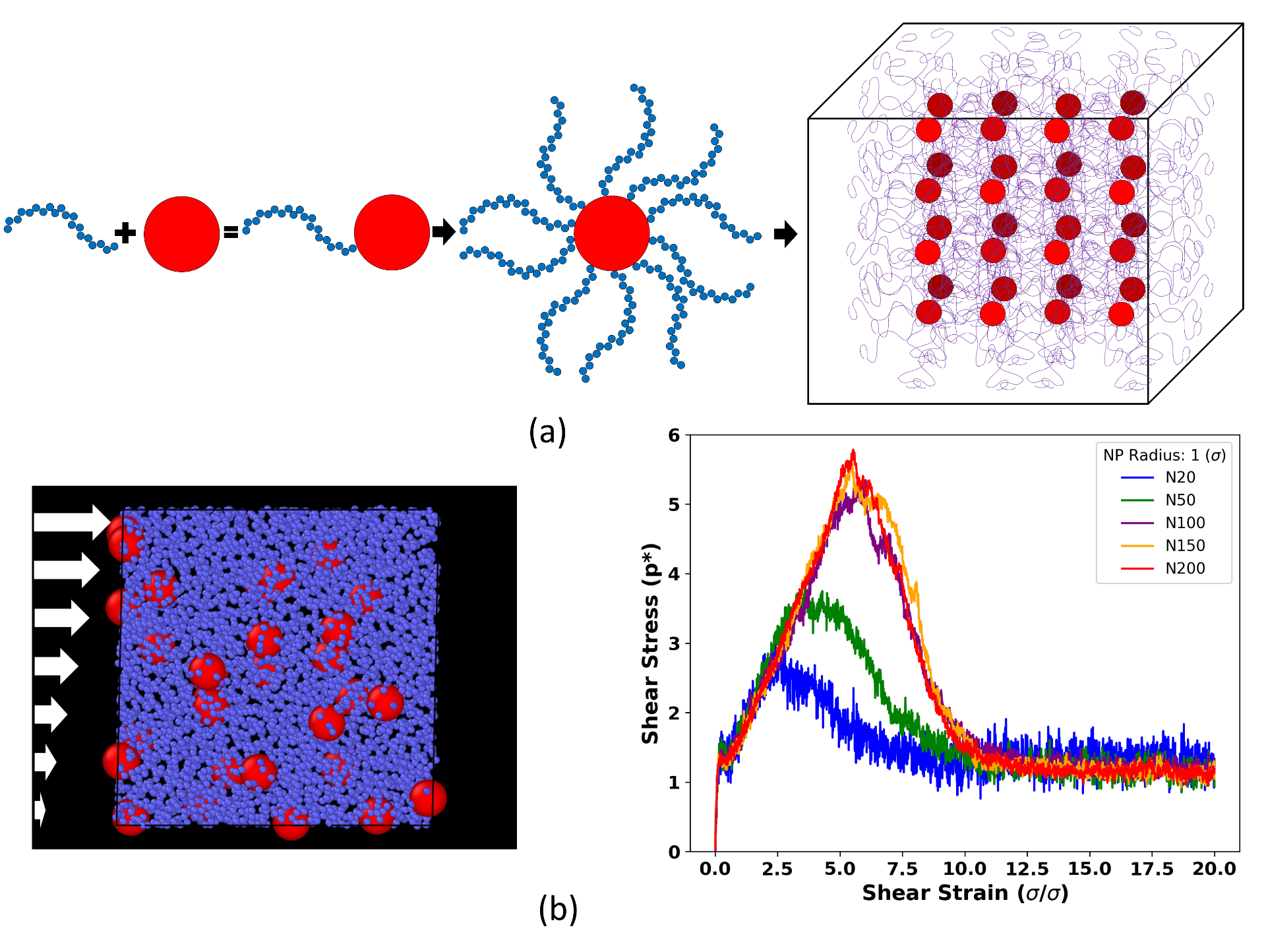
Fig. (a) visual aid for the structure of a PGN and the well dispersed matrix created when assembled into a continuous material (b) molecular dynamics simulation applying a shear strain to a PGN composite system, along with the resulting stress data for systems with differing grafted polymer arm lengths